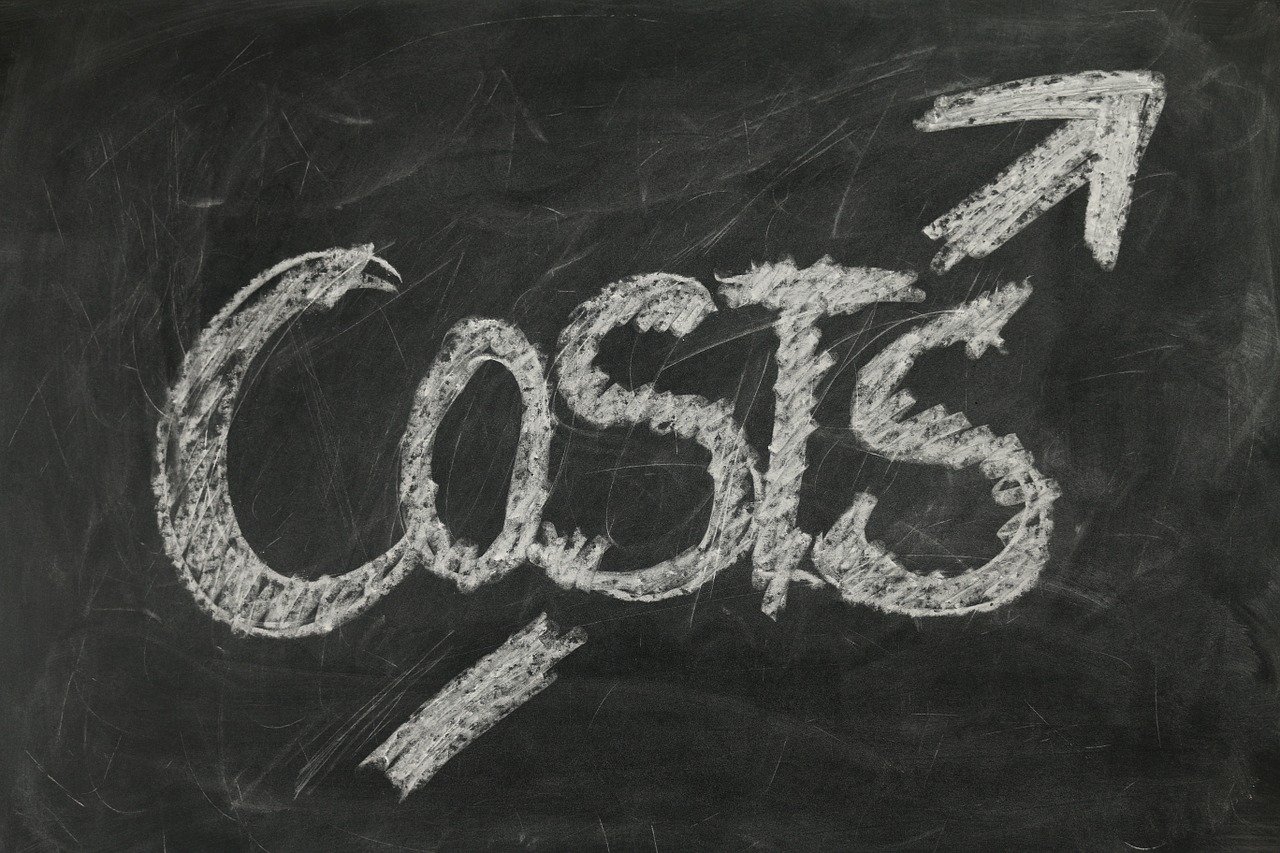
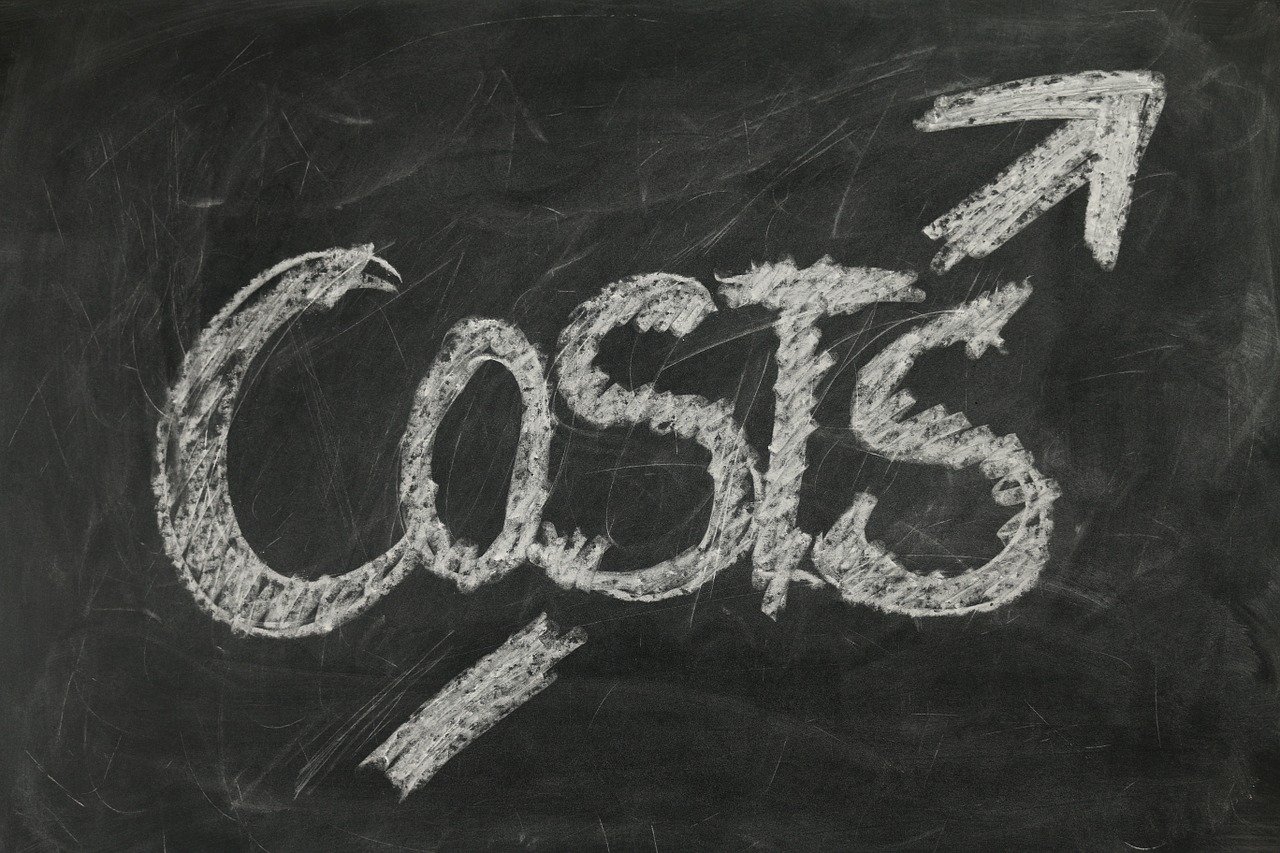
In the landscape of financial management, direct costs stand out as one of the key players. However, if you are new to running a business, you might not quite understand exactly what they are and why they are so integral to your financial health. This is what we will explore in this article.
What is a direct cost?
A direct cost is an expense that is directly associated to a particular product, service, project, or activity. These expenses are usually accrued during the production of goods or the delivery of products and services.
These costs are often variable, meaning they fluctuate in direct proportion to the level of production or the amount of services provided.
Get started with our forecasting software so that you can plan your business' futureManage your direct costs in Brixx
Why are direct costs important?
Direct costs are crucial in financial management for several reasons:
Ensuring accurate costs
By identifying and tracking direct costs, you and your business can ensure accuracy in calculating the true expense associated with a specific product or delivering a particular service. This is essential for realistic financial reporting.
Analyse business profitability
Direct costs play a crucial role in determining the profitability of individual products or services. By understanding the direct costs involved, businesses can make informed decisions about pricing strategies and easily allocate to maximize profits.
Control your business costs
Monitoring direct costs allows businesses to have better ownership over their production or service delivery processes. This allows them to implement cost-saving measures and improve overall efficiency.
Improve business decision making
Understanding your direct costs is essential for business decision-making. Businesses can assess financials and make informed decisions on resource allocation based on a clear understanding of these costs.
Planning and budgeting
Direct costs are essential in budgeting and financial planning. Businesses can create realistic budgets and forecasts by accounting for the direct costs associated with their activities.
In summary, direct costs provide a brilliant understanding of the financial aspects of production and service delivery.
How to calculate direct costs
Calculating direct costs involved calculating and adding up all expenses directly linked to making a specific product or providing a particular service. Here’s a general guide on how to calculate direct costs:
1. Identify all instances of direct costs
These can include:
- Any raw materials, such as those used in manufacturing
- Any labour costs, including wages and benefits for employees
- Any costs related to manufacturing, such as supplies and components
- Any direct expenses that can account for other costs, such as shipping costs
2. Gather your cost data
Ensure that you collect detailed records of expenses related to the above identified direct cost categories. This could include reviewing salaries and invoices.
3. Calculate your individual direct costs
For each direct cost category, calculate all relevant expenses during a specific period.
4. Sum up your total direct costs
Combine the direct costs to calculate the total costs associated with the production of the product or service.
5. Exclude any indirect costs
Ensure that only costs directly tied to the product or service are included. Exclude any indirect costs, which are expenses that cannot be clearly traced to a specific cost object.
6. Use Activity-Based Costing (ABC) if required
In some cases, businesses may employ activity-based costing to understand and allocate indirect costs more accurately. However, for the calculation of direct costs, the focus is on those expenses directly tied to the product or service.
7. Make sure to review and adjustments
Regularly review and update your direct cost calculations to account for any changes in expenses or production processes. This ensures ongoing accuracy in financial reporting.
Example Calculation:
Suppose you’re calculating direct costs for a toy manufacturing business. The direct costs may include the cost of raw materials, direct labor for workers on the production line, and specific supplies used in manufacturing.
- Raw materials: $10,000
- Labour costs: $15,000
- Manufacturing costs: $5,000
- Total Direct Costs = $30,000
This total represents the direct costs associated with producing the widgets during the specified period.
What are some examples of direct costs?
We have already listed some examples of direct costs. See more below:
- Raw materials: For example, the cost of materials used in the manufacturing of a product.
- Employee labour: This can include manufacturing workers, construction workers, or service providers.
- Manufacturing costs: Costs related to specific supplies and components used in the production process.
- Direct expenses: Other costs directly tied to a particular project or product. For instance, shipping costs for a product.
- Commissions: Sales commissions can be considered a direct cost.
- Direct utilities: Utilities costs directly associated with the production process, such as electricity or water used in manufacturing.
- Materials for services: Direct costs may include materials directly related to providing a service. This might include specialized software.
- Marketing costs: If marketing expenses are directly tied to promoting a specific product or service, they can be considered direct costs.
- Travel costs: If travel is directly related to a specific project or product, it can be considered a direct cost.
Identifying and tracking these direct costs is absolutely essential for businesses to accurately assess the true expenses associated with their business.
Direct costs vs indirect costs
Direct costs are directly tied to a specific product or service. Their association with cost is clear. In contrast, indirect costs are general expenses necessary for overall business matters, and often involves estimation and apportionment.
Understanding the distinction between direct and indirect costs is crucial for accurate cost accounting, pricing strategies, and financial decision-making within a business.
Direct costs
- Definition: Direct costs are expenses that can be specifically and easily traced to a particular business instance (e.g. product or service).
- Examples: These costs are typically tangible. Examples include raw materials and direct labor.
- Traceability: Direct costs can be attributed to a cost object, providing a clear link between the cost and the product or service.
- Variability: Direct costs often vary proportionally with the level of production or the amount of services provided.
Indirect Costs:
- Definition: Indirect costs are expenses that cannot be directly linked to a business instance.
- Examples: These costs are often overhead expenses that support overall operations, such as rent or utilities.
- Allocation: Indirect costs are attributed to products or services using methods like overhead rates, as they are not easily traceable to a specific cost object.
- Variability: Indirect costs may not vary in direct proportion to production levels and are often considered fixed costs.
Are there any challenges in direct costs?
There are several challenges associated with managing and calculating direct costs in business. Here are a few examples:
Accurate cost allocation: Ensuring that costs are accurately allocated can be challenging. The complexity arises when a single cost item may contribute to multiple products or activities.
Overhead allocation: Determining the appropriate method for allocating indirect costs can be challenging. Incorrect allocation methods may lead to distorted cost figures and affect decision-making.
Fluctuating market costs: Direct costs can fluctuate due to a variety of reasons, such as market conditions. Predicting and managing these fluctuations can be a challenge for businesses.
Integration with technology and software: Integrating technology and software for tracking and managing direct costs can be challenging. Businesses may face issues with data accuracy, system compatibility, and employee training.
Any change in production processes: If a business undergoes changes in production processes, accurately attributing direct costs to these changes can be complex.
External factors: Economic conditions, global events, and changes in regulations can impact the availability and cost of direct inputs, affecting overall cost structures.
Accuracy and consistency of data: Ensuring the accuracy and consistency of data related to direct costs is critical.
Inconsistent data or errors in recording can lead to inaccurate financial analysis and decision-making.
Highlighting direct costs in Brixx
Brixx shines as a valuable financial forecasting tool within the financial world, especially when it comes to highlighting direct costs.
With Brixx, businesses can easily see and understand the expenses directly linked to making specific products or offering services. Our user-friendly platform helps break down the complexities of managing costs, allowing businesses to pinpoint and focus on expenses related to their main activities. Whether it’s raw materials or labor, Brixx makes it simple to examine direct costs in detail. This not only helps businesses make smart decisions but also streamlines production and improves overall financial performance.
With Brixx, the emphasis on direct costs becomes crystal clear, providing a straightforward view of the financial landscape and supporting strategic decision-making based on accurate data. Take a free 7-day trial to see the benefits for yourself.